Plumbing is a demanding career that requires a lot of hard work and dedication. However, it can also be a very rewarding career for those who are willing to put in the time and effort to become a plumber.
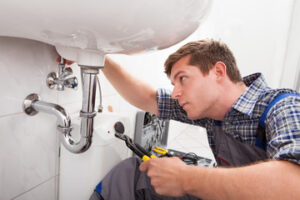
Plumber Aurora CO installs, repairs, and maintains plumbing systems in residential and commercial settings. They also interpret blueprints and ensure that plumbing projects meet local building codes and regulations.
Test cocks, also called valves, are an essential part of backflow testing. They are used to identify the type of backflow preventer assembly and its overall function and direction of water flow. They are numbered and attached to the backflow assembly. Testers are required to follow specific tests and procedures when examining the valves and reading the gauges. Test cocks can also be used to flush out the body of the backflow preventer during a maintenance or repair service.
For example, a double check assembly (DCV) consists of an input shut off valve; two independently working spring-loaded, check valves; and four test cocks. During backflow testing, each of these test cocks is opened and closed to verify that both of the check valves are functioning properly. This will help to prevent backflow leakage and ensure that the city’s water supply remains safe.
The test cocks are located on the inlet and outlet of each of the two check valves. They are also found on the relief valve diaphragm and upstream of the upstream and downstream shut off valves. It is important to flush the cocks before and after pressurizing your test kit to make sure no dirt or debris is introduced into the gauge, which could affect its accuracy. To avoid this, you can use a special tool called the Test Cock Wrench that fits perfectly with Deringer and Magnum devices.
Pressure gauges
During backflow testing, pressure gauges monitor the pressure of water and air in tanks and systems. If the pressure differs from what it should be, the plumber will note the difference and take the appropriate action to correct the problem. Pressure gauges are very important for backflow testing because they allow the tester to verify that check valves prevent backflow, air ports open when they should and relief valves open before the pressure builds too high. This allows the tester to verify that all parts of a system are functioning as they should and that any errors in the testing are due to equipment malfunction or human error rather than a backflow issue.
A pressure gauge consists of a flexible measuring element, an indicator and a case. The measuring element is an elastic tube that moves in response to a change in pressure. This movement is translated into a rotary motion that drives the pointer and scale face of the gauge so we can read the reading. Currently, there are three different types of elastic elements used in mechanical pressure gauges: diaphragms, bellows and transducers. The type of gauge that best meets the needs of a particular application depends on the operating conditions, installation environment and desired accuracy.
The indicators of pressure gauges are either directly connected to the movement of the elastic element or indirectly connected via a range spring. Those that are directly connected (as in the bellow design) cause the needle on the scale to move immediately in response to a pressure change. The range spring in a diaphragm gauge, on the other hand, causes the needle to move linearly in proportion to the differences between two pressures.
Finally, the case of a pressure gauge is designed to protect the sensitive components inside. The most common cases are made of thermoplastic, aluminum or stainless steel. Some models offer an internal pressure relief plug feature that vents the case in the event of a pressure overload.
Whether to choose an analog or digital display, a solid front gauge or open front gauge and the size of the dial are other features that need to be considered when choosing a pressure gauge. The location of the threaded mount and how it will be mounted also dictates the gauge’s use. For example, if the gauge is going to be used in an area where it may be hard to see, then a larger dial might be a good choice.
Check valves
Check valves are a vital part of piping systems that provide a cost-effective solution to basic backflow prevention. They are easy to install and operate, and can be used in a variety of applications and working conditions. However, their performance can be compromised by improper selection and installation. This is why it’s important for plumbers to understand the basics of check valve design and function.
There are many different types of check valves, but they all operate the same way: a movable component allows flow in one direction and blocks it in the opposite direction. Depending on the style, this movable component can be a disc, plate, ball, or hinged element. The most common type is the swing check valve, which uses a hinged disc that opens when pressure increases and stays open when the system pressure decreases. Other types include the lift, wafer, center guided, and dual plate check valves.
The main reason for installing check valves is to prevent back siphonage, which can occur when a non-potable source of water enters the public water supply through the spout of a municipal backflow preventer. This can cause contamination of the potable water supply and result in expensive clean-up costs.
To avoid this, the city has installed hundreds of new check valves on water pipes in high-rise buildings and other vulnerable locations. These valves are designed to stop the leaking of non-potable water from fire hydrants and other sources.
Check valves are also effective in preventing water hammer, which can damage piping and equipment. This condition occurs when a fast change in velocity causes a sudden closure of a valve or other obstruction. The resulting pulses in the fluid cause a large increase in pressure that can damage pipes and equipment.
To avoid this, plumbers should use a non-slam check valve alongside an end damper to reduce the pressure changes caused by the closing of a valve. They should also ensure that the valve is at least 10 pipe diameters upstream of the point where it will be located. This distance will allow a nice laminar flow through the valve and help to prevent premature wear.
Relief valves
When a backflow preventer’s pressure drops or when the check valve fails, the relief valve is there to keep the system from overpressure. The relief valve can be set to open at a pressure lower than the system’s maximum operating pressure. The set pressure is determined by determining the system size and flow rate. It is important to install the correct type and size of relief valve to handle the system’s expected load.
The design of the pressure-relief valve depends on the application and can include different configurations of internal parts to withstand different pressure ranges. Many codes and standards around the world address the design of pressure relief valves. The most widely recognized is the ASME Boiler and Pressure Vessel Code. It is important to select and install the right pressure-relief valve for a backflow preventer installation.
There are several things that can cause a relief valve to fail to reseat. One is a reduction in the water supply side pressure caused by an outage or by a high demand from activities such as fire fighting. The other is a failure of the second check valve due to a leak, which allows the higher pressure from the customer side to go past the failing second check valve and act on the relief valve diaphragm. This causes the relief valve to open and discharge.
Another reason is the overpressure of the piping upstream of the valve, which can cause the relief valve to rapidly cycle, or chirp, in response to the pressure loss. This occurs when the pressure at the relief valve inlet decreases during the flow below the reseat point, then quickly rises to the reseat point once the flow stops. This rapid cycling can also occur when the reseat point is too high.
To reduce the chance of overpressure in critical process applications, it is common practice to install two relief valves. They are typically piped in parallel and have “car sealed” full-port ball or gate block valves on the inlet and outlet of each valve. These block valves are car sealed to keep them open when the relief valve is in operation and closed when the valve is removed for maintenance. Another option is to use an ASME-approved selector valve, which simplifies the operation of the relief valve and eliminates the need for a car seal when the valve is in service.